Articles
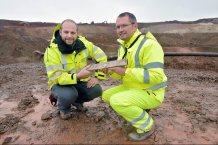
James McFarlane Senior Mine Geologist at Wolf Minerals with Dr Robin Shail from the Camborne School of Mines.
New mine proves focal point for geological research in South West
Drakelands Mine has become the focal point for a series of new locally and regionally significant research projects which will increase the understanding of the rich and fascinating geology of South West England.
The £140 million Drakelands project opened in September 2015, making it Britain’s first new metal mine in 45 years and once again putting the UK back on the world map as a metals exporter.
Wolf Minerals is working with leading institutions including Camborne School of Mines, Plymouth University and the British Geological Survey on geological and mineralogical studies of the Hemerdon tungsten and tin deposit, on which the mine is located, and which will feed into broader research of the South West’s geology.
Dr Colin Wilkins, Economic Geologist at Plymouth University, is leading a project with two of the University’s 4th year postgraduate students on the geology of the Hemerdon deposit and the mineralogy of its granite and host rocks.
Wolf is also collaborating with Dr Robin Shail and Professor Mark Smethurst, of the University of Exeter’s Camborne School of Mines, on the Tellus How Innovation Project funded by the National Environment Research Council (NERC). This helps local businesses make the most of data generated during the £1.7 million Tellus South West survey in 2013-14 focussed on the region’s geology, resources, landscape and ecosystems.
In addition, Dr Simon Tapster and Eimear Deady of the British Geological Survey are also undertaking research on radiometric dating and characterising the hydrothermal fluids associated with mineralisation of the Hemerdon Granite.
James McFarlane, Wolf Minerals senior mine geologist, said: “The Hemerdon deposit and indeed the broader South West England mineral province has a long and interesting past, both geologically, historically and in more recent times through some of the modern exploration undertaken.
“In terms of the mining and processing operation here at Drakelands, whilst we already have a significant amount of historical and new data it is vital that we continue to gather and interpret as much information as possible. This enables the geological team to further refine our knowledge of the deposit, and with more information we understand more and are able to make more intelligent decisions.
“We are delighted that our work here has enabled new partnerships to be formed and new areas of research to be opened up which will benefit not only the work of Wolf Minerals but also add to the wider understanding of the geology and mineral resources of this unique part of the world.”
Dr Robin Shail, of Camborne School of Mines, said: “We had our first MSc student working with Wolf over summer 2015 during the run-up to first production. It is now an exciting time as mining progresses and exposes previously unseen geology that helps us all try to further understand the combination of processes that have contributed to the formation of this world-class ore deposit.”
Dr Colin Wilkins, Economic Geologist at Plymouth University, said: "This is a fantastic opportunity for two fourth year Plymouth University Geology students to be involved in an industry-focused project, and one that has direct relevance to furthering the understanding of a world-class resource development project here in Devon."
The £140 million Drakelands Mine was officially opened on September 17th 2015, creating about 220 direct jobs and becoming the first new British metal mine in 45 years.
With an estimated production of 5,000 tonnes per annum of tungsten concentrate and 1,000 tonnes of tin concentrate, Drakelands will be one of the world’s most important tungsten mines, producing about 3.5% of forecast global demand, providing a secure supply of tungsten – which is regarded as a critical mineral by the UK, US and EU – and pumping hundreds of millions of pounds into the South West and UK economies over the next decade.
The construction phase generated significant economic benefits with up to 500 people on site and an estimated 70 per cent of the £75 million cost of the process plant was spent with UK companies, many in Devon and Cornwall.
Date: 24 March 2016